L’amélioration de l’efficience des flux de production consiste à augmenter la part des opérations à valeur ajoutée dans le flux. Identifier ce qui est de la valeur ajoutée, signifie qu’il est donc indispensable de qualifier les attentes des clients (externes et internes). Sur cette base, il devient alors aisé d’identifier les différents gaspillages présents dans le flux pour les réduire. A défaut, le risque est de se focaliser sur l’accélération des temps de valeur ajoutée quand ceux-ci ne représentent qu’un temps infime du lead time.
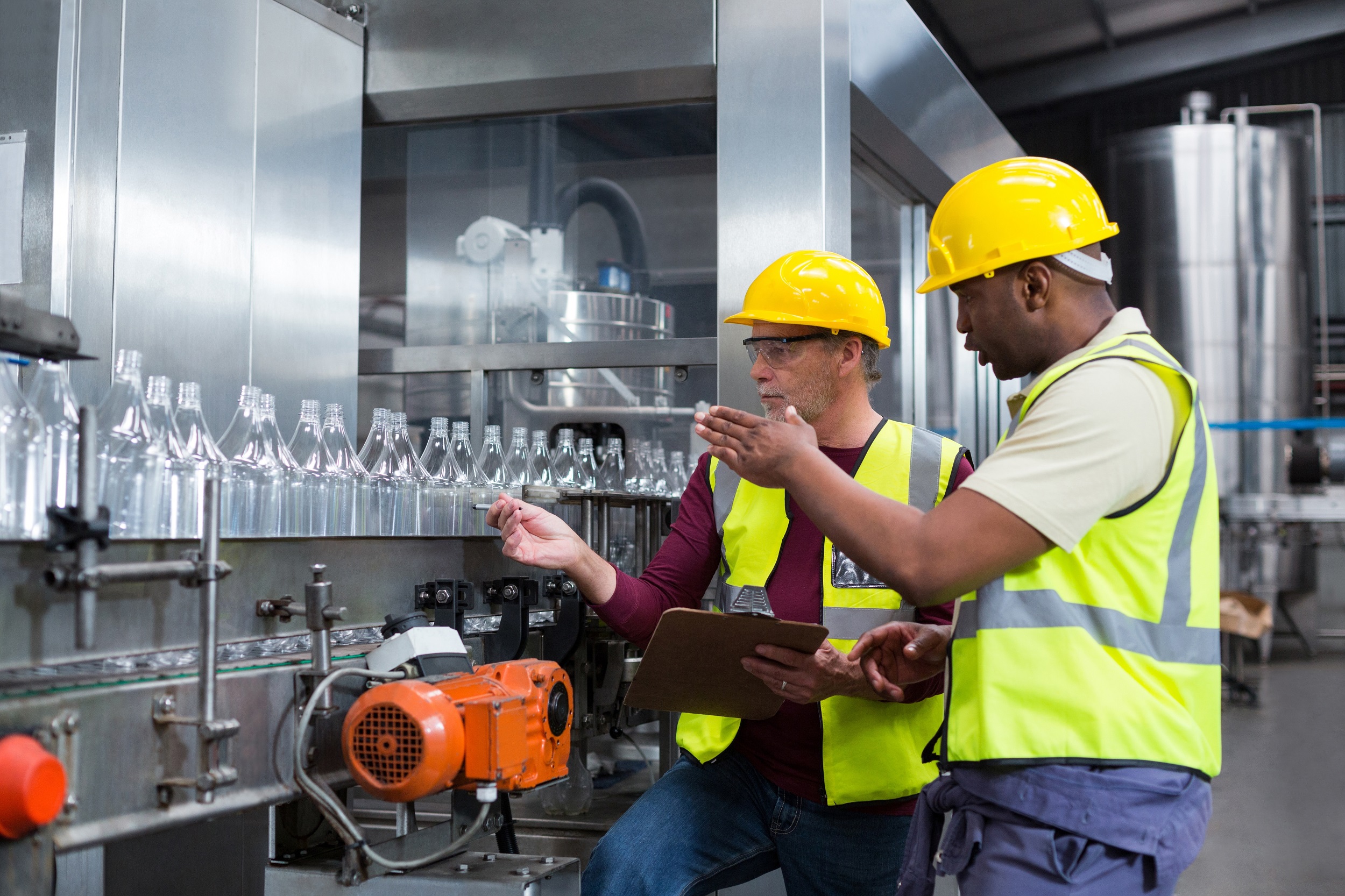
L’amélioration de l’efficience est une démarche transversale dont le bénéficiaire est le flux en faisant en sorte de l’accélérer. Les phases de préparation de la production (plan industriel et commercial, industrialisation, nomenclature, gammes, approvisionnements matière et outillages) sont tout aussi importantes que la production elle-même. L’efficience de la production en est en grande partie dépendante. Enfin, accélérer un flux consiste à accélérer un flux plus qualitatif en travaillant sur la réduction des non-conformités.
Les défis et enjeux
L’enjeu est de produire puis de livrer au client le bon produit, au bon endroit, au bon destinataire, dans les délais convenus avec le juste nécessaire de ressources : ressources en moyens de production (taux d’utilisation des équipements), en matière et composants (réduction des pertes matières et des produits non conformes) et en main d’œuvre (temps de préparation, temps de réglages, temps de production, temps de contrôle).
Améliorer l’efficience consiste à accélérer le flux en identifiant puis en réduisant les gaspillages tout au long du processus industriel pour tendre d’une logique de l’efficacité vers une logique de l’efficience.
Les bénéfices sont mesurables sur les 4 axes de performance (Sécurité/Sérénité, Qualité, Délais, Coûts).
- Sécurité/Sérénité : Si les collaborateurs travaillent avec moins d’irritants quotidiens, parce que ceux-ci auront été captés puis traités, il en découlera une spirale vertueuse permettant de développer la culture de l’amélioration continue. Cela contribue à l’amélioration des conditions de travail et augmente l’attractivité de l’entreprise.
- Qualité : Il n’y a aucun sens à accélérer un processus défectueux ! Travailler sur la réduction de la non-qualité pour tendre vers le bon du premier coup (jidoka) permettra de réduire les réclamations clients, de réduire les coûts induits et d’accélérer le flux en évitant le retravail nécessaire pour compenser les rebuts, les tris ou les retouches.
- Délais : Accélérer le flux permet de réduire le lead time entre commande et livraison. Le délai perçu par le client peut donc être diminué pour devenir un facteur différenciant par rapport à la concurrence.
- Coûts : Les ressources étant mieux utilisées et les gaspillages diminués, les coûts variables sont réduits en conséquence. Un flux mieux maitrisé permet de réduire les encours et donc les niveaux de stocks au bénéfice de la trésorerie. La capacité dégagée par la meilleure utilisation des équipements, permet soit de diminuer les coûts en réduisant les transports exceptionnels et les heures supplémentaires, soit de récupérer de la capacité de ventes permettant d’amortir les coûts fixes.
Les principes clés
Impliquer tous les acteurs dans la cartographie des processus permettra de comprendre le fonctionnement et les pratiques du moment avant de déterminer une cible partagée.
Cette cible permettra de construire une feuille de route en priorisant les actions ayant le plus d’impact :
- Amélioration des processus d’anticipation charge/capacité par approche PIC/PDP,
- Identification des goulots et amélioration de leur TRS (taux de rendement synthétique) par plusieurs typologies de chantiers,
- Amélioration de la planification et de l’ordonnancement,
- Réduction des encours par étude d’équilibrage des opérations et mise en place de flux tirés (séquenceur, kanban, …),
- Visualisation des en-cours et des temps d’attente à chaque étape dans le flux en temps réel en utilisant des solutions digitales type Business Intelligence, MES, AIC digitales,
- Amélioration des flux physiques par études d’implantations,
- Etudes d’opportunités d’innovation et d’intégration de briques technologiques (intégration de cobots, robots, utilisation IA, …).
Les phases
1 - Compréhension/vérification des besoins clients
2- Caractérisation du périmètre d’étude :
- Cartographie de la situation actuelle,
- Cartographie de la valeur des flux de production (approche VSM),
- Cartographie des flux transversaux et administratifs,
- Cartographie des déplacements physiques par diagramme spaghetti,
- Analyse de déroulement des opérations sensibles.
3 - Cartographie du flux cible
4 - Plan d’action hiérarchisé
5 - Coaching et conduite de chantiers
Les facteurs clés de succès
Disposer d’une stratégie de développement claire afin d’aligner le plan d’amélioration et travailler sur les flux les plus pertinents.
Impliquer tous les acteurs de terrain (ceux qui réalisent) et les sponsors :
- En phase de cartographie du flux initial pour capter la réalité du terrain et pas celle des procédures.
- En phase de construction du flux cible.
Cette approche permettra d’intéresser les acteurs aux enjeux et de les impliquer dans la mise en œuvre d’une vision partagée.
Planifier les chantiers et anticiper les besoins de libération de ressources (équipements, équipes, prestataires).
Organiser les agendas des équipes pour réaliser, tester, mettre au point et valider les solutions.
Prévoir un budget « amélioration » pour ne pas bloquer certaines opportunités non budgétées.
> Voir nos cas clients :
Technisub Italie - Rossignol - Routin - Sames